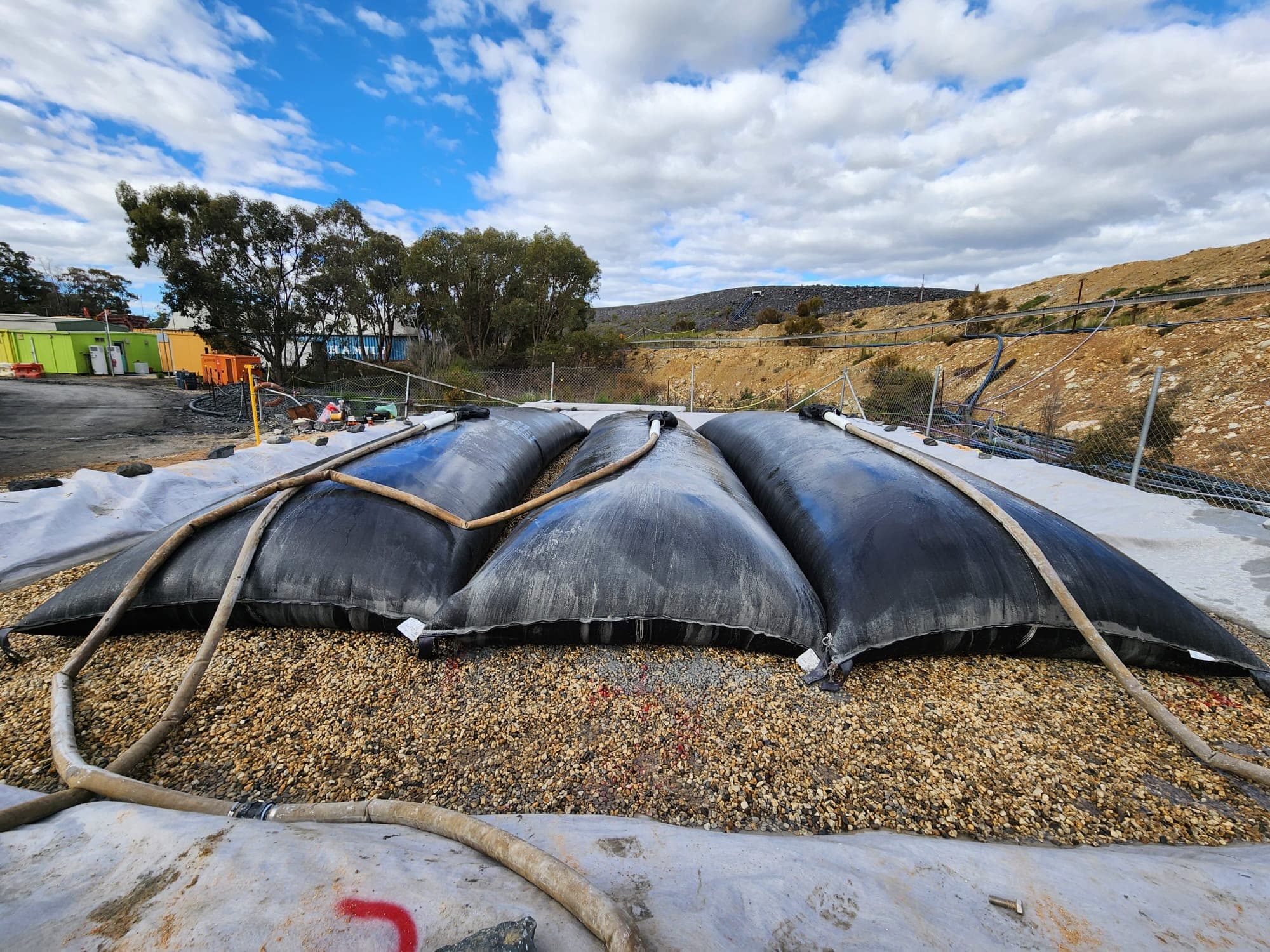
How can mining companies effectively manage dewatering challenges and implement innovative solutions for mine waste management?
Sludge ponds are critical for various industries, especially in mining, for managing process waste. However, closing these ponds poses challenges due to the sludge's low bearing capacity. A multi-functional geotextile reinforcement layer provides a robust solution for capping these ponds, enhancing their closure process.
This guide explores the engineering principles behind this solution through six comprehensive steps.
The geotextile reinforcement layer improves the effective bearing capacity of the sludge, prevents fill loss into the sludge and requires no pre-treatment of the contained sludge.
The first two steps will determine the design inputs for the engineering.
Step 1: Assessing sludge characteristics
Understanding the sludge's undrained shear strength is crucial. Detailed geotechnical reports and in-situ vane shear tests help tailor the reinforcement solution to the pond's specific conditions, including the sludge's location (above or below water) and its pH, ensuring compatibility with the geotextile material.
Required sludge characteristics:
Undrained shear strength of the sludge
Location of sludge surface
pH or chemistry of the sludge.
This will determine:
The solution used
The strength grade and seam strength
The construction method
The material durability.
We also wish to know the location of the sludge (ie. above water or below water) as this influences the construction process. Where the sludge is beneath a water layer, specific techniques can be used to install the reinforcement layer (eg. pulling geotextile panels across, placement by barge etc).
Knowing thepH of the sludgewill confirm the compatibility of the sludge with the polymer of the geosynthetic reinforcement layer. This is generally only a concern for sludges with extreme pH.
Step 2: Evaluating site materials and resources
Identifying the types of cover material and construction equipment available is essential. This step influences the design by determining the imposed loads on the geotextile layers and the feasibility of placing cover material without disturbing the sludge.
Knowing the available resources such as the:
Characteristics of the cover layer
Construction equipment available at site
Technique for fill placement.
Will determine the:
Strength grade required
The overlap distance or the seam strength.
For remote sites, the construction equipment available may be limited.
Some sites will be able to place the cover material without having machinery or people traversing the sludge, however this is not always possible (particularly for large ponds in remote areas, such as mine sites).
Step 3: Determining pond dimensions
The size and shape of the pond dictate the most efficient method for delivering and installing the geotextile reinforcement, whether in rolls or pre-sewn panels, to minimize waste and ensure a seamless application.
There are two common construction techniques:
Rolls of geotextileare supplied to site and installed across the pond surface. To minimise wastage, roll dimensions may be selected to suit the specific pond. The geotextile rolls are pulled across the pond to form a continuous reinforcement layer. Consideration needs to be given to number of reinforcement layers and overlaps should settlement be expected.
Geotextile panelscan be created by sewing rolls into panels (either on-site or in the factory) to allow pulling or floating across the pond as a single layer.
Step 4: Designing the reinforcement layer
The design phase confirms the appropriate strength grade of the geotextile and the layout of the reinforcement layer, utilizing tension membrane principles to address potential failure modes and ensure stability as the sludge deforms under the load of the cover material.
Stressing geotextile reinforcement by first constructing parallel fill “fingers” across sludge pond surface (prior to infilling with remaining fill). The shear strength of sludge increases as pore water pressures dissipate through the geotextile panels.
Tension membrane principles are used for the design process. There are several papers that outline a suggested design process for this application, and established design software can also be used to check on the local and global failure modes:
Stabilization of very soft clay using geofabric - Bengt B.Broms (1987)
Design and construction of geosynthetic reinforced lagoon caps - D.B. Andrews and G.N. Richardson (1999)
Reinforcement design for construction of cover soil over soft sludge - R.D. Espinoza and P.J. Sabatini (2008)
Capping/Closure of sludge ponds - S.M. Gale, A. Theroux, B. Lacina and J. Henderson (2008)
Step 5: Managing transportation and handling
Producing and transporting the geotextile material requires careful planning to ensure safety and efficiency. This step covers the logistics from factory to site, emphasizing safe handling practices throughout the process.
Experience brings an understanding of the safe handling options along the delivery process:
During the factory production or fabrication process.
Packing and unpacking of the finished product into the shipping containers at factory and destination.
If required, how to load and unload the finished product onto trucks for transportation to remote site.
Handling of the finished product at site, including placement into the final position.
Step 6: Installation considerations
Successful installation is the result of thorough planning and collaboration between the installer and supplier. Proper handling and placement techniques are critical for a smooth construction process and the project's overall success.
Conclusion:
Closing sludge ponds with geotextile reinforcement is a complex but manageable process that benefits significantly from expert guidance. Our team of specialists is ready to assist you with tailored solutions for your sludge pond closure needs.
The finished geotextile product should be unloaded adjacent to the ponds. If installing geotextile panels, then these are to be unfolded prior to initial placement.
Project success requires a detailed understanding of the construction process, applications knowledge, technical expertise and advanced manufacturing capabilities.
References:
Geotextile Reinforced Sludge Pond Closures brochure
Reinforced Mine Tailings Pond Closure, Huelva, Spain case study
Capping/Closure of sludge ponds technical paper
Stabilization of very soft clay using geofabric :Bengt B.Broms (1987)
Capping/Closure of sludge ponds :S.M. Gale, A. Theroux, B. Lacina and J. Henderson (2008)
Geotextile Reinforced Sludge Pond Closures brochure
Geotextile Reinforced Sludge Pond Closures brochure
Capping/Closure of sludge ponds technical paper
Reinforced sludge capping layer, Harbin City case study