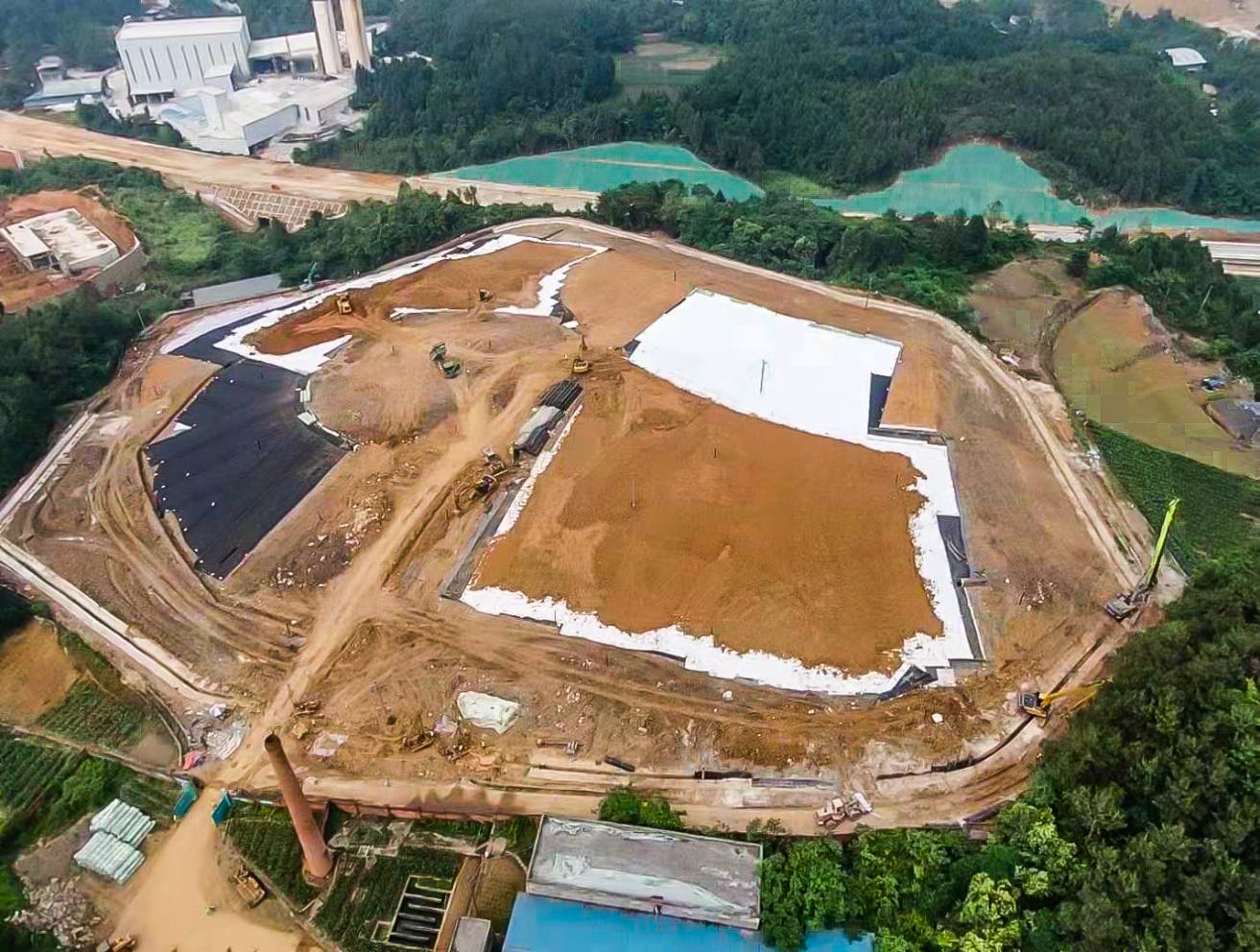
How to prevent toe leakage in flexible vertical barrier walls
Vertical barrier systems block lateral migration of subsurface fluids such as fresh water, salt water, methane gas, and contaminated leachates from waste piles or leaking containments into surrounding environments.
To effectively counter the migration characteristics of pollutants and groundwater, and comply with environmental codes and standards, the vertical barrier wall needs to be installed in the micro-weathered bedrock layer – which forms a natural water barrier or impermeable layer.
The Solmax CurtainWall flexible vertical barrier system is a type of cut-off wall system composed of an HDPE membrane impermeable layer and a chemical grouting curtain. The vertical barrier system contains pollutants within a specified area.
To prevent the diffusion of pollutants through the bedrock fissures from causing toe leakage in the flexible vertical barrier wall, several factors need to be considered.
After the HDPE geomembrane is installed in the excavation trench, the HDPE liner is embedded in the impermeable bedrock layer. Usually, this needs to be at least 1 m (3 ft) below the impermeable layer. Then, a special sealant is injected into the bottom of the trench through the chemical grouting process. This effectively connects the flexible HDPE liner with the bedrock, improving its impermeability.
The liner of the vertical barrier wall is designed to be impermeable. It is manufactured according to strict quality standards to ensure high performance. To prevent seepage, it is vital to control the construction quality of the chemical grouting process. This process can present technical challenges because the ‘toe’, the junction between the geomembrane and the impermeable layer, must achieve the expected anti-seepage performance. To perform optimally, the anti-seepage design of chemical grouting at the bottom of the trench needs to consider: the grouting standard, construction scope, grouting material, grout influence radius, drilling layout, grouting pressure, effect evaluation and so on. The properties and formula of grouting materials must meet the basic requirements for environmental protection and restoration of the project:
It bonds with the HDPE liner and with the underground bedrock, even under humid conditions (for example where there is slurry in the trench).
It has good chemical resistance, such as acid and alkali corrosion resistance and can resist microbial erosion.
It has good impermeability after coagulation and curing, and its coefficient is less than 1×10-7 cm/s (1×10-3 in/s).
It has sufficient engineering strength. The tensile and compressive strength of the grouting sealing material needs to be higher than the strength of the material to be bonded.
The grouting sealing material is quick setting. The setting or curing time is adjustable, and the setting process can be completed in the desired time. It has little or no shrinkage when gelled or cured as well as low viscosity, flexible fluidity, convenient material preparation and good on-site constructability.
The bonding material is stable and durable. Under normal temperature, normal pressure, and underwater environmental conditions, its basic properties remain unchanged, and does not crack easily.
The chemical grouting materials used have different material compositions and formulas. Some have high-quality sodium bentonite, Portland cement, sand, sodium silicate, and polymer to mix into grouting materials. The composition depends on the requirements of the specific project.
Sometimes, a modified epoxy resin is used. High-strength Portland cement and selected coarse sand are added to increase the performance of the modified epoxy resin.
The chemical grouting material best suited for the project working conditions should be selected. The construction quality of the grouting process needs to be controlled so to avoid toe leakage in the flexible vertical barrier wall. Finally, it ensures that the vertical barrier system provides stable and effective waste containment.
Explore more blogs
View allHow to combine engineered earth armoring with greywater treatment
Resilient water management by combining greywater recycling with engineered earth armoring for irrigation, erosion control, and increased property value.
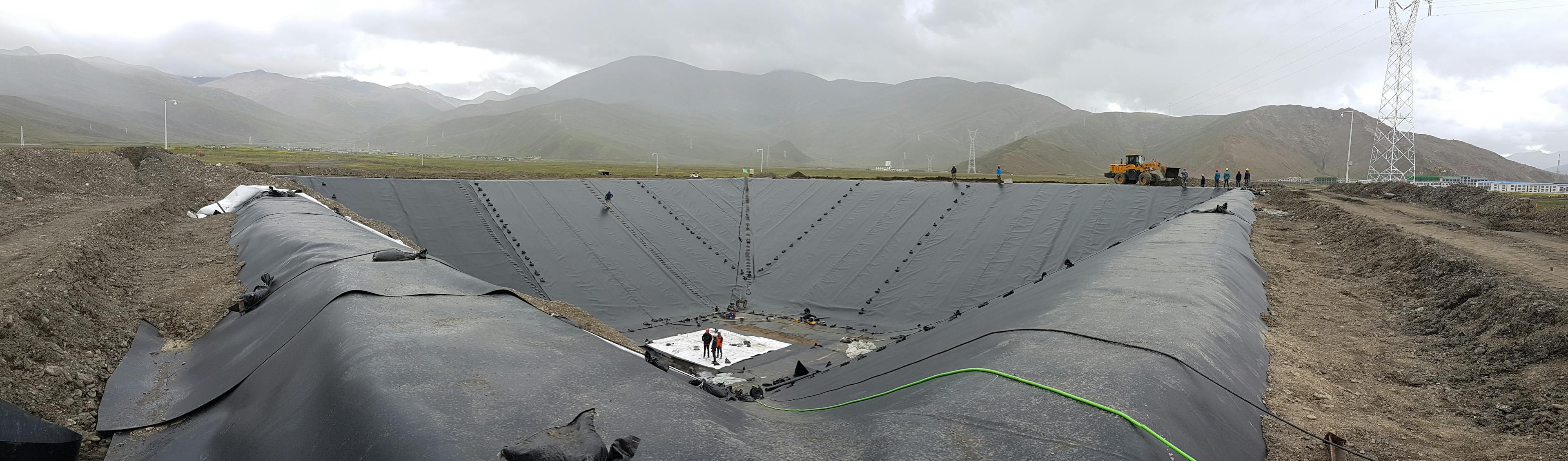
How can geosynthetics help energy transition?
Geosynthetics accelerate agricultural outputs and improve resilience by optimizing water management through enhanced irrigation efficiency and providing structural stability to agricultural infrastructures like dams and reservoirs.
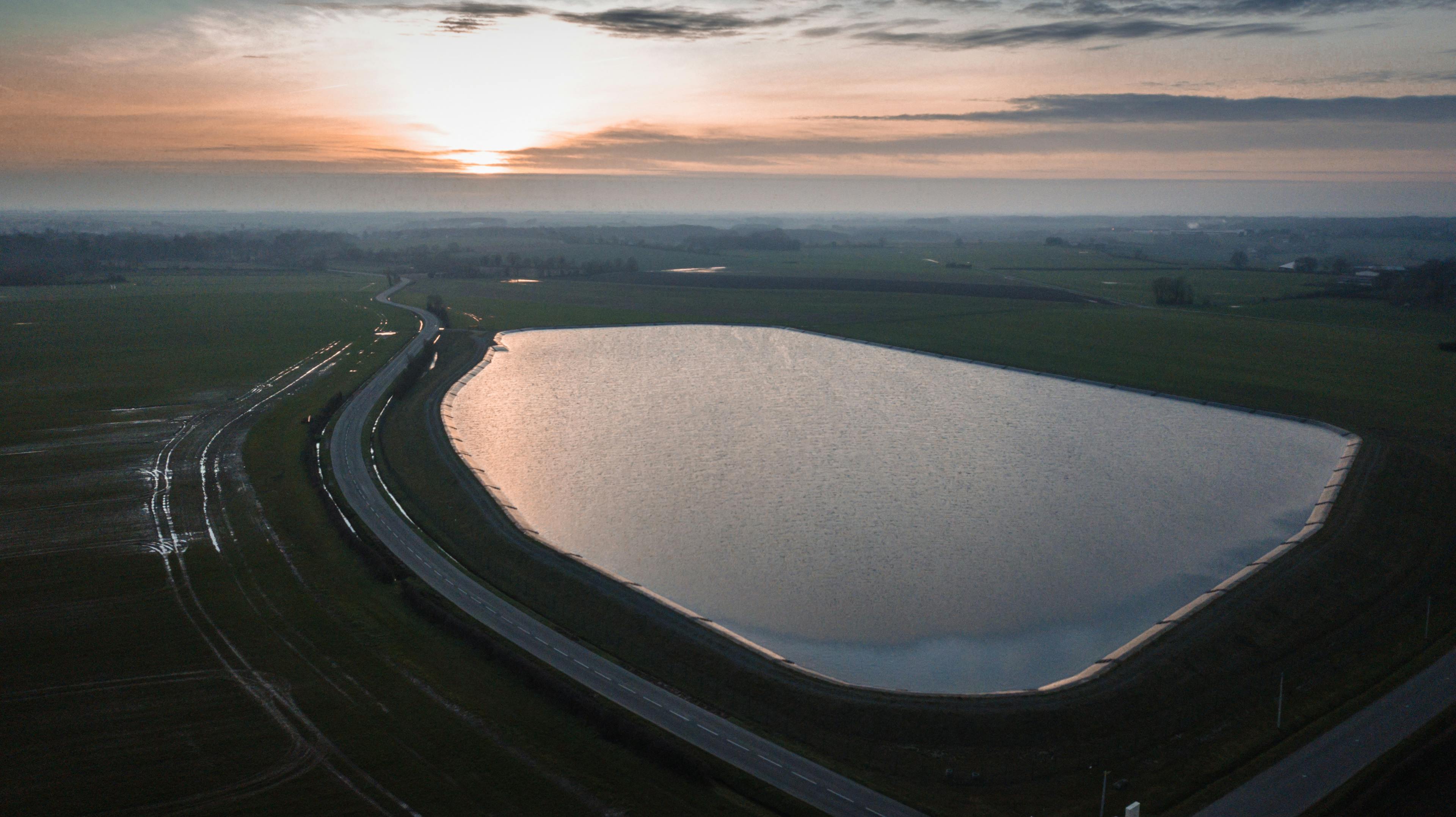
How can geosynthetics accelerate agriculture outputs and improve resilience?
Geosynthetics accelerate agricultural outputs and improve resilience by optimizing water management through enhanced irrigation efficiency and providing structural stability to agricultural infrastructures like dams and reservoirs.