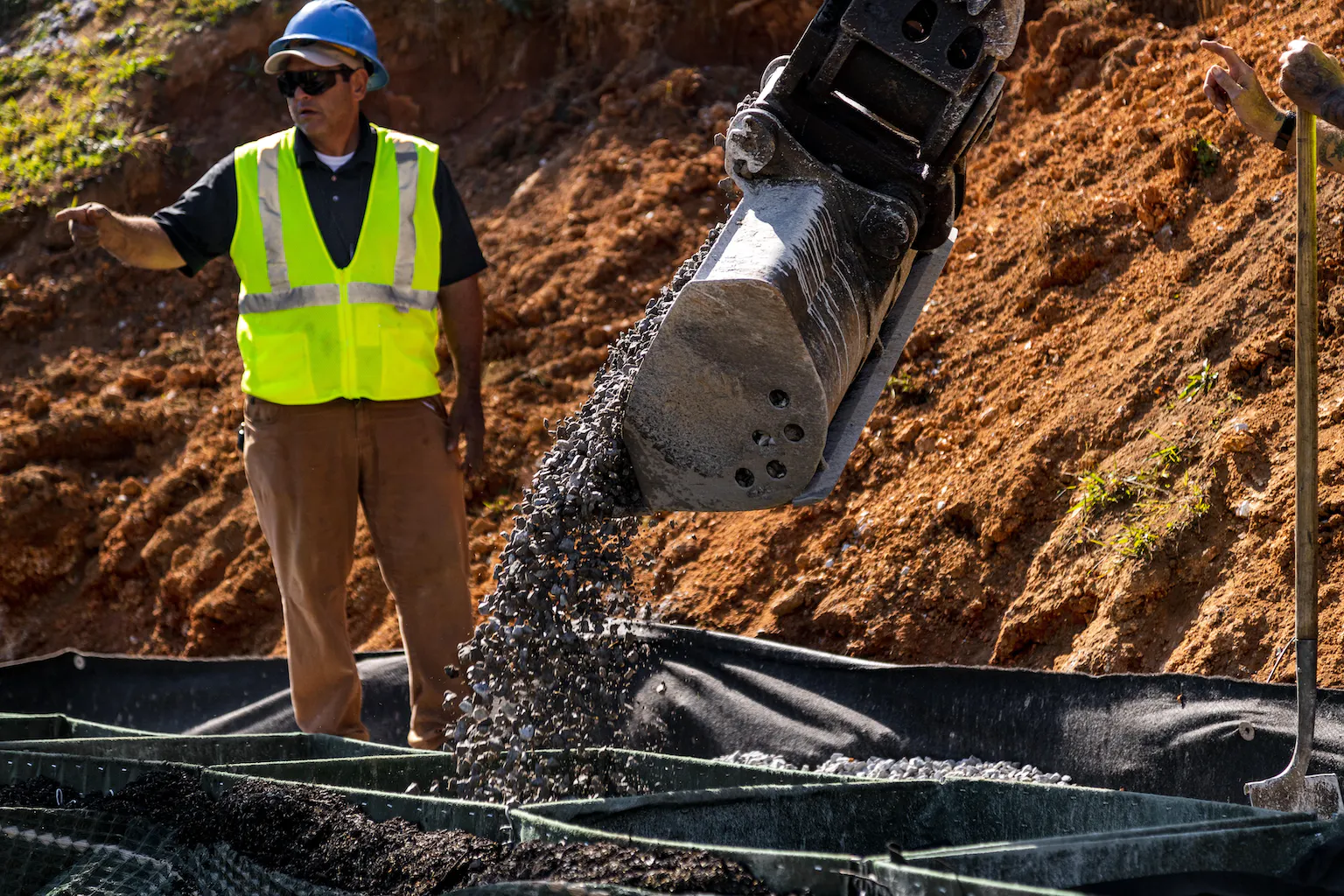
How to engineer a gravity wall system
Gravity retaining walls
Gravity retaining walls utilize the wall system's weight to counteract the earth's pressures from the soil it retains. Commonly used walls are made from rock-filled gabions or interlocking concrete blocks weighing 1,800 lbs (815 kg) or more. These walls can be built up to 12-feet high (3.6 meters) using a wider base or by increasing the offset distance between layers.
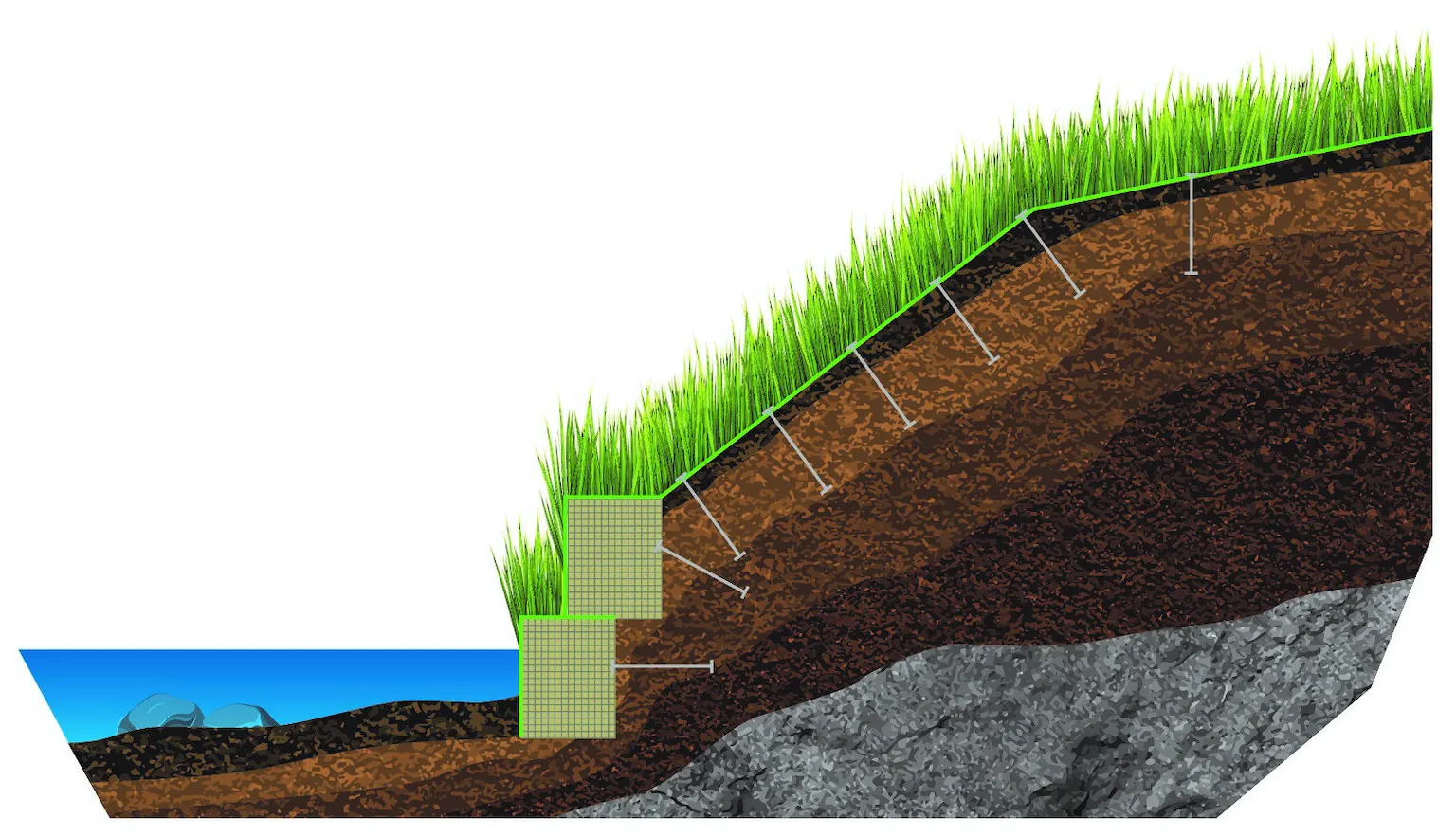
Recently, as site conditions permit, designers prefer vegetated facades over traditional concrete or rock-filled systems. To cater to this need, PROPEX® Scourlok® was introduced, offering vegetated facing using PROPEX Pyramat® high-performance turf reinforcement mat (HPTRM) combined with soil-filled wire bastions.
While primarily designed for stream channels and lake shorelines, PROPEX Scourlok can also be used for non-water retaining walls.
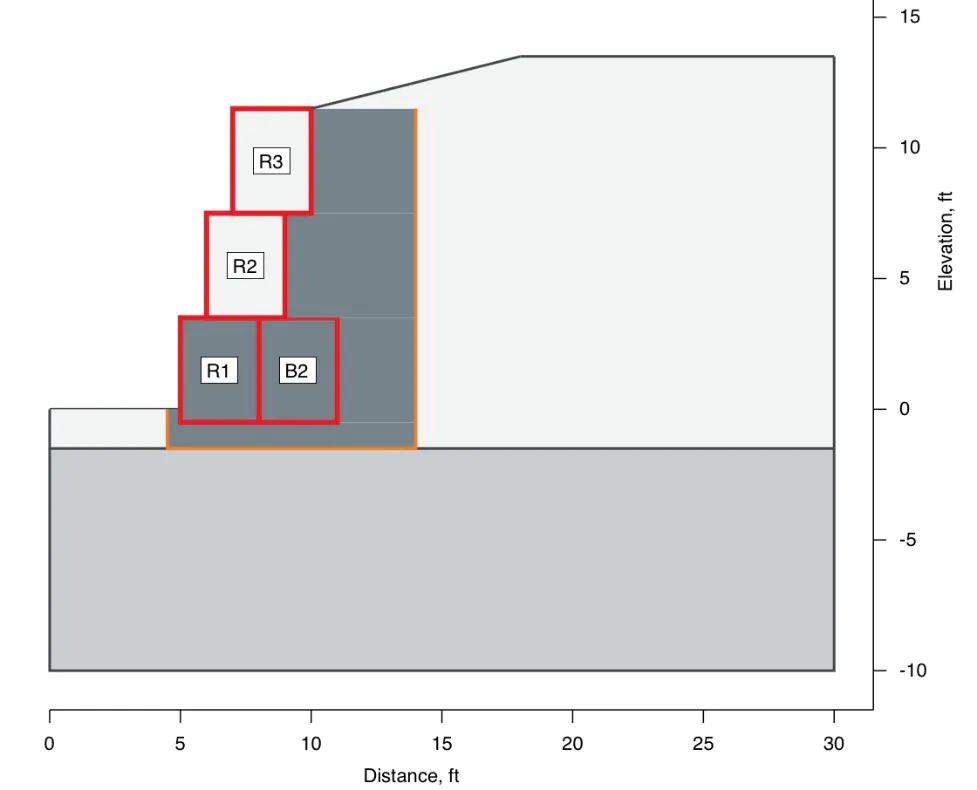
Components & features
PROPEX Scourlok is made of PROPEX Pyramat 75 HPTRM and interlocking, galfan coated steel baskets lined with GEOTEX® geotextile.
Designed for organic growth media, its pockets and tops promote vegetation.
One unit has 5 cells, each 3 x 3 x 4 ft, making a total 15-ft long unit.
These units can connect and stack in different configurations.
Shipped flat, they can be expanded and filled on-site with soil or gravel.
The PROPEX Pyramat wrap aids in vegetation growth and ensures the system's durability.
Walls can be built up to 12-feet high; higher walls require a wider base to ensure safety.
Installation details
PROPEX Scourlok must be placed on native soil or approved fill. Foundation preparation involves removing topsoil to expose native soil and creating a trench for the first bastion row. Moisture-sensitive soils may require a gravel leveling pad and drainage. For water-prone sites, PROPEX Scourlok's base can be filled with coarse gravel.
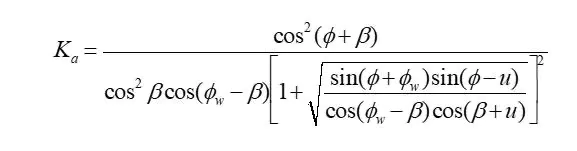
Soil infill for PROPEX Scourlok should:
Match specific Unified Soil Classification System (USCS) criteria.
Have a maximum particle size of 3 inches.
Contain no harmful substances.
Minor curves of up to a 30-ft radius are feasible. Tighter curves require field adjustments. Proper soil compaction is vital for longevity.
Geotechnical design principles
The PROPEX Scourlok system must resist lateral earth pressure from retained soil. This pressure, alongside additional forces, is computed using Coulomb's active earth pressure coefficient. These forces must be counteracted by the weight of the wall units. Additional analysis ensures the system's long-term stability. Ground anchors or the PYRAWALL® system can be alternatives based on site conditions.
Often, a gravel backfill is placed behind PROPEX Scourlok to allow groundwater drainage, enhancing wall stability.
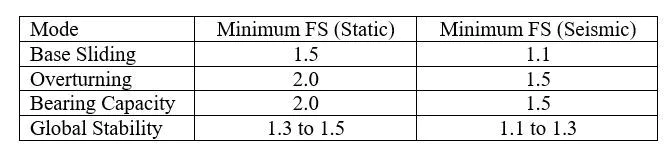
Conclusion
The combination of PROPEX Pyramat 75, galfan coated steel baskets, and GEOTEX geotextile provides a versatile gravity-wall system suitable for various stabilization needs. Its transportability is an edge, especially for remote or challenging sites. As with all construction projects, thorough site investigation, and continuous oversight are essential for success.
References
Miller, S.M. (2017). Applications of geosynthetic wrap-face vegetated walls. Geosynthetics 35(4): 24-33.
NCMA. Design Manual for Segmental Retaining Walls, 2nd Ed.; 1996.
Explore more blogs
View allHow to combine engineered earth armoring with greywater treatment
Resilient water management by combining greywater recycling with engineered earth armoring for irrigation, erosion control, and increased property value.
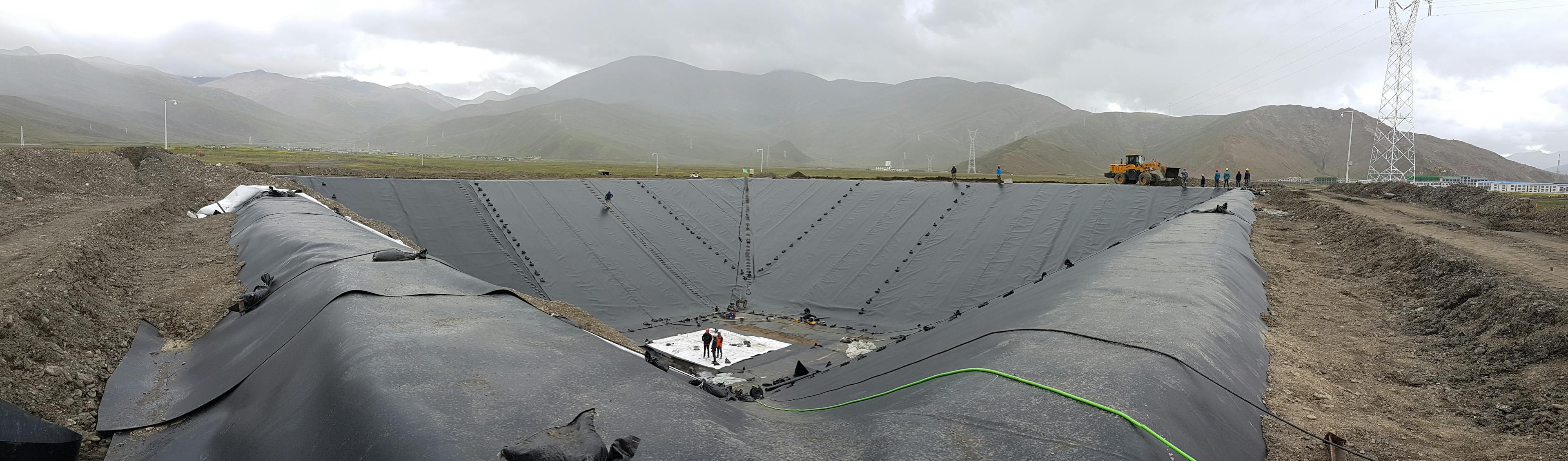
How can geosynthetics help energy transition?
Geosynthetics accelerate agricultural outputs and improve resilience by optimizing water management through enhanced irrigation efficiency and providing structural stability to agricultural infrastructures like dams and reservoirs.
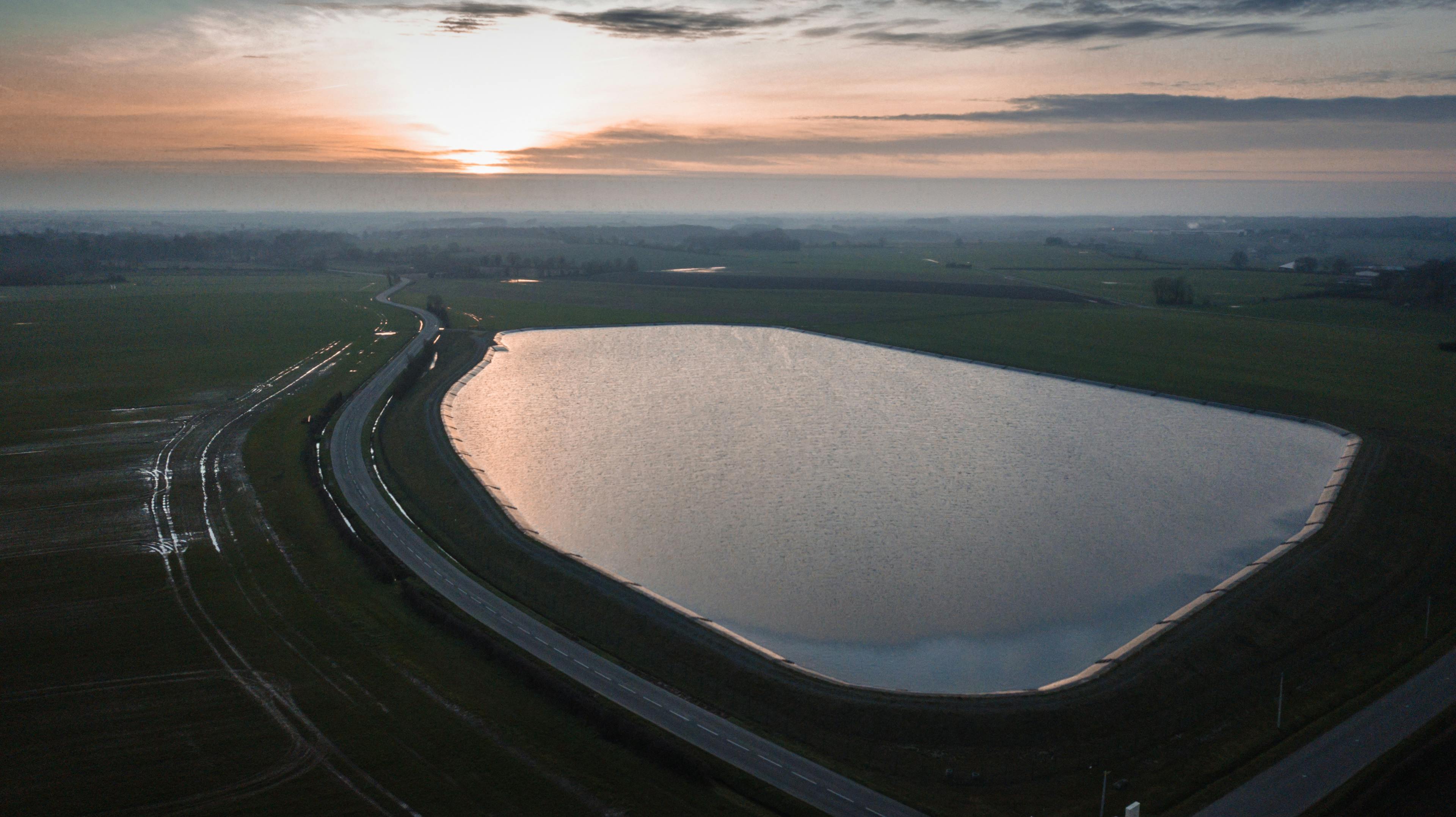
How can geosynthetics accelerate agriculture outputs and improve resilience?
Geosynthetics accelerate agricultural outputs and improve resilience by optimizing water management through enhanced irrigation efficiency and providing structural stability to agricultural infrastructures like dams and reservoirs.